Емкости СПГ в металлургии — прорыв в тяжелой промышленности
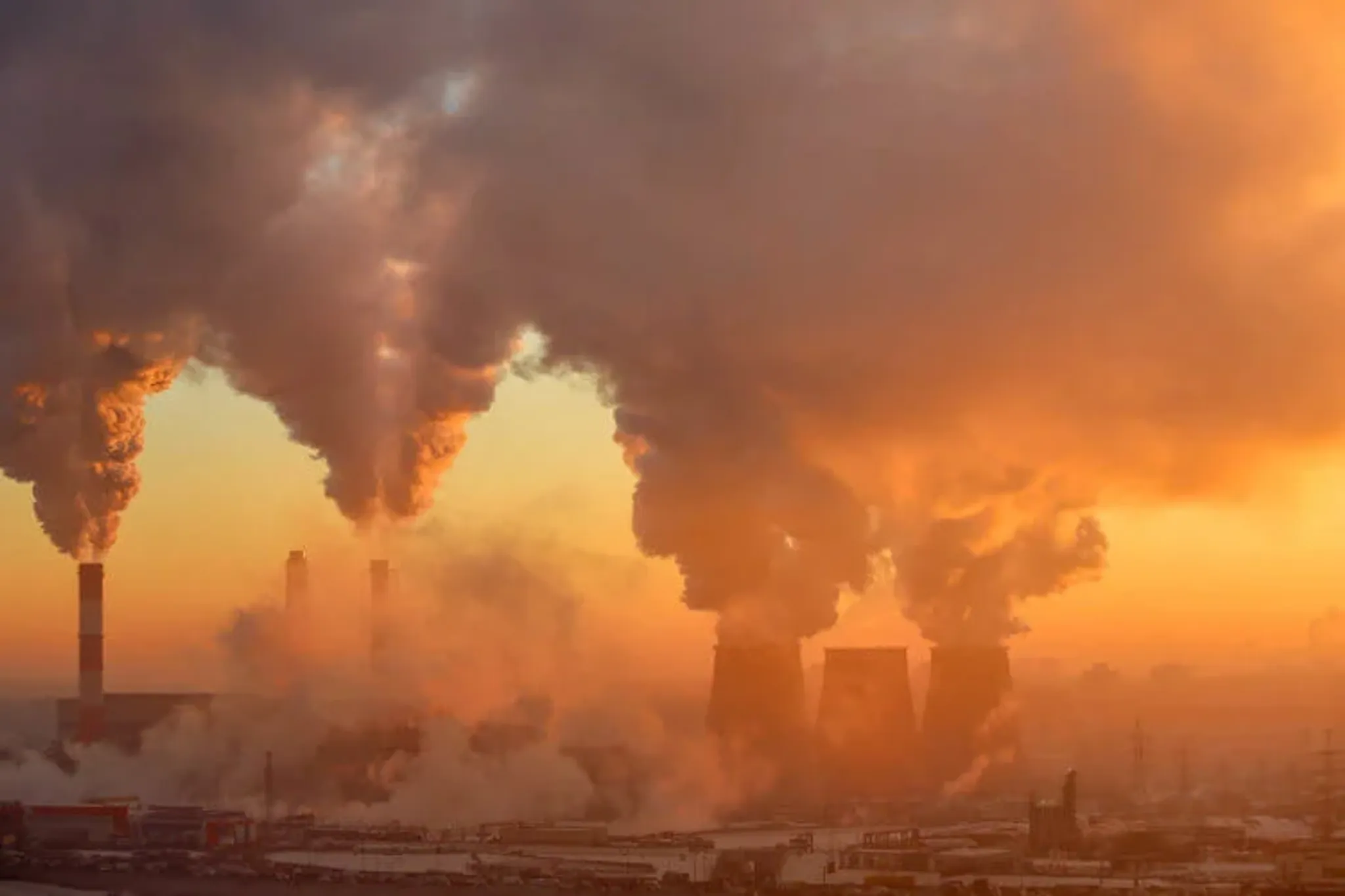
Металлургия, столетиями державшаяся на угле и коксе, сегодня стоит на пороге революции. Глобальный тренд на декарбонизацию, ужесточение экологических норм (например, Европейский «Зеленый курс») и растущие штрафы за выбросы CO₂ заставляют гигантов индустрии искать альтернативы. Сжиженный природный газ (СПГ) оказался в центре этого перехода: он не только сокращает углеродный след на 20–30%, но и дает технологическую гибкость, недоступную традиционным энергоносителям.
Однако ключевым звеном в этой цепочке стали не сами газовые горелки или печи, а емкости для СПГ — сложные инженерные системы, без которых невозможны ни хранение, ни транспортировка топлива. Эти криогенные резервуары, выдерживающие температуры до −162°C, превращают газ в «мобильный» ресурс, позволяя заводам работать даже в регионах без газопроводов. Например, в Сибири, где морозы достигают −50°C, или в австралийской пустыне, где СПГ заменяет дизель в электрогенерации.
Зачем металлургии СПГ?
Металлургия, как отрасль с многовековой историей, всегда зависела от «грязных» энергоносителей — угля и кокса. Однако в эпоху климатических вызовов и ESG-требований (экология, социальная политика, управление) эти ресурсы стали обузой. По данным Международного энергетического агентства (МЭА), на производство стали и алюминия приходится 9% глобальных выбросов CO₂ — больше, чем все автомобили мира вместе взятые. Это ставит отрасль под удар регуляторов: к 2030 году углеродные налоги в ЕС вырастут до €100 за тонну CO₂, а к 2050-му многие страны планируют полностью отказаться от угля.
СПГ становится спасательным кругом — он не только сокращает углеродный след, но и сохраняет рентабельность. При сжигании природный газ выделяет на 40–50% меньше CO₂, чем уголь, и почти не образует токсичных частиц (сажи, оксидов серы). Например, японская компания JFE Steel после перевода двух доменных печей на СПГ снизила выбросы на 1,2 млн тонн CO₂ в год — эквивалент посадки 20 млн деревьев.
СПГ дает металлургам три ключевых преимущества:
Энергетическая независимость. Заводы в регионах без газопроводов (как канадский Algoma Steel или норвежский Mo i Rana) больше не зависят от дорогого дизеля или угля. СПГ доставляется автоцистернами или по железной дороге и хранится в криогенных резервуарах, обеспечивая запас топлива на месяцы.
Гибкость производства. Газовые горелки позволяют точнее регулировать температуру плавки, что улучшает качество стали. На заводах Thyssenkrupp в Германии переход на СПГ увеличил выход высоколегированных марок металла на 15%.
Инвестиционная привлекательность. Компании, внедряющие СПГ, получают доступ к «зеленым» кредитам и грантам. В 2023 году ArcelorMittal привлек €500 млн от ЕБРР на модернизацию печей под газ, сократив процентную ставку за счет ESG-рейтинга.
Как СПГ меняет индустрию
Германия: Thyssenkrupp и переход на «чистую» сталь
Немецкий концерн Thyssenkrupp в Дуйсбурге, крупнейший сталелитейный завод Европы, начал замену угля на СПГ в 2022 году. Для этого были установлены стационарные резервуары объемом 25 000 м³ с двойной вакуумной изоляцией. Результаты:
Снижение выбросов CO₂ на 500 000 тонн в год (25% от общего объема завода).
Повышение эффективности плавки за счет точного контроля температуры газовых горелок.
Проект получил €200 млн финансирования от ЕС в рамках программы «Зеленый курс».
Южная Корея: POSCO и водородно-СПГ гибрид
POSCO, крупнейший металлургический гигант Азии, в 2023 году запустил пилотный проект в Пхохане. Здесь СПГ смешивают с «голубым» водородом (полученным из газа с улавливанием CO₂).
Гибридные резервуары вместимостью 10 000 м³ снизили выбросы на 70% по сравнению с углем.
Технология позволила POSCO выйти на рынок «зеленой стали» для европейских автопроизводителей (Volvo, BMW).
ОАЭ: Emirates Steel и газ вместо мазута
В Абу-Даби завод Emirates Steel полностью отказался от мазута, переведя плавильные печи на СПГ. Для этого построили подземное хранилище объемом 40 000 м³, защищенное от экстремальных температур пустыни.
Сокращение выбросов: 1,2 млн тонн CO₂ в год.
СПГ поставляется с месторождения Шах (ADNOC), что снизило затраты на логистику на 30%.
Бразилия: Ternium и СПГ для восстановления лесов
Компания Ternium в штате Рио-де-Жанейро использует СПГ не только для металлургии, но и для восстановления экосистем.
Резервуары модульного типа (20 единиц по 300 м³) питают печи и обеспечивают энергией питомники по выращиванию деревьев.
Каждый год проект компенсирует 200 000 тонн CO₂, связывая выбросы через посадку 5 млн саженцев.
Япония: Kobe Steel и аварийные резервы
После землетрясения в Фукусиме (2021) Kobe Steel внедрила систему аварийных резервов СПГ.
5 подземных резервуаров по 5000 м³ обеспечивают автономную работу завода 14 дней.
Решение предотвратило остановку производства во время кризиса 2023 года, когда газопроводы были повреждены тайфуном.
Австралия: BlueScope Steel и СПГ для удаленных шахт
BlueScope Steel использует мобильные СПГ-хранилища для снабжения рудников в пустыне Пилбара.
Автоцистерны с криогенными резервуарами доставляют газ на 2000 км, заменяя дизель в генераторах.
Экономия: $15 млн в год на топливе, сокращение выбросов на 25 000 тонн CO₂.
Швеция: H2 Green Steel и безуглеродное будущее
Стартап H2 Green Steel строит в Бодене первый в мире завод, где СПГ используется как переходное топливо перед полным переходом на водород к 2030 году.
Гибридные резервуары (СПГ + водород) снижают текущие выбросы на 90%.
Инвесторы: Mercedes-Benz, Scania, Altor (объем вложений — €2,5 млрд).
Китай: HBIS Group и мега-резервуары в провинции Хэбэй
Китайская HBIS Group, второй по величине производитель стали в мире, в 2022 году запустила СПГ-терминал с резервуарами объемом 80 000 м³ рядом с заводом в Таншане.
Газ заменил 40% угля в доменных печах, сократив выбросы CO₂ на 1,8 млн тонн в год — как если бы с дорог исчезли 350 000 автомобилей.
Проект стал частью национальной программы «Синее небо», направленной на борьбу со смогом в промышленных регионах.
Резервуары оснащены системой рекуперации холода: испаряющийся газ охлаждает воду для технологических циклов, экономя 5% энергии.
Казахстан: АО «АрселорМиттал Темиртау» и газ вместо угля
Карагандинский металлургический комбинат в Казахстане, принадлежащий ArcelorMittal, с 2021 года использует СПГ для плавки стали.
4 модульных резервуара по 1000 м³ обеспечивают 30% энергопотребления завода.
Выбросы оксидов серы (SOₓ) упали на 90%, что критично для региона с тяжелой экологической обстановкой.
СПГ поставляется с Тенгизского месторождения, сократив логистические расходы на 20% за счет отказа от импорта угля.
Узбекистан: АГМК и СПГ для модернизации
Алмалыкский горно-металлургический комбинат (АГМК) в 2023 году запустил пилотный проект по замене мазута на СПГ.
2 стационарных резервуара по 5000 м³ питают медеплавильные печи.
Себестоимость меди снизилась на 12%, а выбросы твердых частиц — на 70%.
Проект поддержан Азиатским банком развития ($150 млн кредита под 2% годовых).
Россия: «Норникель» и утилизация попутного газа
Норильский никель реализовал уникальный проект: попутный газ, ранее сжигавшийся в факелах на нефтяных месторождениях, теперь сжижается и поставляется на металлургические заводы компании.
3 криогенных резервуара по 15 000 м³ в Норильске обеспечивают 100% потребности плавильных цехов в энергии.
Результаты:
Утилизация 500 млн м³ газа в год (ранее это были чистые потери).
Сокращение выбросов CO₂ на 1,1 млн тонн ежегодно.
Продажа углеродных квот принесла компании $25 млн дополнительной прибыли.
Проект окупился за 3 года и стал моделью для других сырьевых гигантов России.
Китай: Baowu Steel и мобильные решения для Синьцзяна
Baowu Steel, крупнейший сталелитейный конгломерат мира, в 2023 году развернул в Синьцзяне сеть из 20 мобильных резервуаров СПГ.
Каждый модуль объемом 300 м³ питает плавильные печи и генераторы электроэнергии.
Завод в регионе с нулевой газовой инфраструктурой сократил зависимость от угля на 60%.
Система позволила избежать штрафов ЕС за углеродный след экспортной стали на сумму €50 млн в год.
Беларусь: БМЗ и СПГ в условиях санкций
Белорусский металлургический завод (БМЗ) в Жлобине из-за санкций на импорт угля из ЕС перешел на СПГ, поставляемый из России.
Железнодорожные цистерны-газовозы доставляют сжиженный газ с завода «Портовая» (Санкт-Петербург).
Установлены 2 резервуара-накопителя по 2000 м³, что снизило себестоимость проката на 8%.
Проект стал примером импортозамещения в условиях геополитического кризиса.
СПГ vs Водород: почему газ пока выигрывает?
Хотя «зеленый» водород называют топливом будущего, его массовое применение в металлургии отложено до 2040–2050 годов из-за дороговизны и технологических барьеров. СПГ же — доступное промежуточное решение. Более того, его можно смешивать с водородом (до 20%), как это делает шведский проект HYBRIT. Такие гибридные системы уже сейчас снижают выбросы на 60–70%, не требуя полного переоборудования заводов.
Что тормозит переход?
Главные барьеры — высокие стартовые затраты (криогенные резервуары на 50 000 м³ стоят $50–70 млн) и дефицит инфраструктуры. Но тренд необратим: по прогнозам Goldman Sachs, к 2030 году 30% стали в мире будет производиться с использованием СПГ. А это значит, что емкости для сжиженного газа из узкоспециализированного оборудования превратятся в такой же стандарт металлургии, как доменные печи или прокатные станы.
Какие ёмкости используют в металлургии?
В металлургии выбор ёмкостей для СПГ определяется масштабами производства, климатическими условиями и доступностью инфраструктуры. От гигантских стационарных хранилищ до мобильных модулей — каждая конструкция решает уникальные задачи, сочетая криогенные технологии с требованиями тяжелой промышленности.
Стационарные криогенные резервуары: фундамент крупных заводов
Стационарные резервуары — это основа инфраструктуры СПГ на металлургических гигантах. Их строят вблизи доменных печей или прокатных цехов, чтобы минимизировать потери при транспортировке газа. Такие ёмкости напоминают вертикальные цилиндры высотой до 50 метров, способные вместить до 50 000 м³ сжиженного газа.
Конструкция и материалы:
Двойные стенки: Внутренний слой из нержавеющей стали или алюминия выдерживает экстремальный холод (-162°C), внешний из углеродистой стали защищает от механических повреждений.
Вакуумная изоляция: Пространство между стенками заполнено перлитом или вакуумировано, что снижает испарение газа до 0,05% в сутки.
Системы безопасности: Автоматические клапаны для сброса давления, датчики утечки метана и пожарные барьеры.
Пример: На заводе ArcelorMittal в Гентe (Бельгия) два резервуара по 40 000 м³ обеспечивают 70% энергопотребления предприятия. Их сферическая форма уменьшает площадь поверхности, минимизируя теплопотери
Модульные системы: гибкость для удаленных проектов
Модульные резервуары — это «конструктор» из предварительно собранных блоков, которые можно быстро доставить и собрать даже в условиях вечной мерзлоты или пустыни. Их ёмкость варьируется от 500 до 5000 м³, что идеально для малых и средних предприятий.
Преимущества:
Быстрое развертывание: Установка занимает 2–3 недели вместо 12–18 месяцев для стационарных аналогов.
Адаптивность: Модули можно комбинировать, добавляя новые секции по мере роста потребностей.
Экономия на инфраструктуре: Не требуют сложного фундамента или подводящих газопроводов.
Пример: В Синьцзяне (Китай) Baowu Steel развернула сеть из 15 модульных резервуаров по 1000 м³, что позволило заменить уголь на СПГ без остановки производства
Транспортные цистерны: логистика без границ
Для заводов, удаленных от газовых магистралей, ключевую роль играют транспортные ёмкости. Это могут быть:
Автоцистерны: Вместимостью до 50 м³, используются для регулярных поставок СПГ на малые предприятия.
Железнодорожные танкеры: Перевозят до 120 м³ сжиженного газа, как в проекте Норникеля, где газ доставляют по Северному широтному ходу.
ISO-контейнеры: Стандартизированные криогенные контейнеры (до 40 м³) для мультимодальных перевозок.
Пример: Канадский завод Algoma Steel ежедневно получает СПГ в 20 цистернах, заменяя 800 тонн угля и экономя $1,2 млн в месяц на квотах CO₂ .
Инновационные решения: гибриды и подземные хранилища
Современные тенденции диктуют новые форматы:
Гибридные резервуары: Например, на шведском заводе HYBRIT СПГ смешивают с водородом в резервуарах с мембранными перегородками. Это снижает выбросы на 90% без замены печей.
Подземные хранилища: В ОАЭ Emirates Steel разместила резервуары на глубине 15 метров, чтобы защитить их от 50-градусной жары.
Резервуары с рекуперацией холода: На китайском заводе HBIS Group испаряющийся газ охлаждает воду для технологических циклов, экономя 5% энергии.
Безопасность: как защищают от рисков
В металлургии, где температуры в цехах достигают 1500°C, безопасность резервуаров критична. Для этого используют:
Многослойную изоляцию: До 30 слоев алюминиевой фольги и стеклоткани в вакууме.
Дублированные системы контроля: Датчики давления, газа и температуры передают данные в режиме реального времени.
Аварийные испарители: При отключении энергии газ автоматически сжигается в факельных установках, предотвращая взрыв.
Пример: На заводе Thyssenkrupp (Германия) резервуары оснащены «умными» клапанами, которые за 0,1 секунды блокируют утечку при скачках давления.
Экономика и выгода от СПГ в металлургии
Переход на сжиженный природный газ в металлургии — это не только экологический шаг, но и экономически обоснованная стратегия. СПГ позволяет компаниям снизить операционные расходы, избежать многомиллионных штрафов за выбросы и повысить конкурентоспособность на глобальном рынке. Разберем ключевые аспекты финансовой выгоды.
Снижение затрат на топливо
Хотя СПГ требует инвестиций в инфраструктуру (резервуары, испарители, логистику), его использование часто дешевле традиционных энергоносителей:
Стоимость тонны условного топлива (ТУТ):
Уголь — $120–150,
Мазут — $180–220,
СПГ — $90–130 (в зависимости от региона).
Пример: Завод Tata Steel в Индии после перехода на СПГ сократил ежегодные затраты на топливо на **45млн∗∗,не смотря на первоначальные вложения в резервуары (30 млн).
Почему СПГ дешевле?
Меньше потерь при сжигании: КПД газовых горелок достигает 95%, против 60–70% у угольных.
Снижение логистических издержек: СПГ можно хранить месяцами и доставлять в регионы без газопроводов.
Избежание экологических штрафов
С 2023 года ЕС взимает €100 за тонну CO₂ в рамках системы CBAM («углеродный налог на импорт»). Для металлургических гигантов, экспортирующих в Европу, это означает дополнительные расходы в сотни миллионов долларов. СПГ помогает смягчить удар:
Расчет для завода с выбросами 5 млн тонн CO₂ в год:
При использовании угля: штраф €500 млн/год.
При переходе на СПГ (сокращение на 30%): штраф €350 млн/год → экономия €150 млн.
Кейс: Китайская Baowu Steel благодаря СПГ избежала CBAM-платежей на €220 млн в 2023 году, сохранив доступ на европейский рынок.
Доступ к «зеленому» финансированию
Компании, внедряющие СПГ, получают преференции:
Льготные кредиты: ЕБРР и МБРР предлагают ставки на 1–2% ниже рыночных для ESG-проектов.
Гранты: Программа ЕС «Инновационный фонд» выделяет до €10 млрд на декарбонизацию промышленности.
Пример: ArcelorMittal привлек €500 млн под 3% годовых на модернизацию печей, тогда как рыночная ставка составляла 6%.
Повышение эффективности производства
Газ позволяет точнее контролировать температуру плавки, что улучшает качество металла и сокращает брак:
На заводе Thyssenkrupp (Германия) переход на СПГ увеличил выход высоколегированной стали на 12%, что принесло дополнительно €80 млн/год.
В Норникеле использование СПГ снизило простои печей из-за неравномерного нагрева угля на 25%.
Утилизация попутного газа
Металлургические компании, связанные с добычей ресурсов (как Норникель), могут использовать попутный газ, который раньше сжигался в факелах:
Экономия: 1 млн тонн сжигаемого газа = потеря 50млн(приценеСПГ50млн(приценеСПГ500/тонну).
Кейс: На месторождениях Норильска утилизация попутного газа в резервуарах СПГ принесла $25 млн прибыли за счет продажи квот и экономии на топливе.
Долгосрочные перспективы
Инвестиции в СПГ-инфраструктуру — это «мост» к водородной экономике:
Резервуары можно модернизировать для хранения водорода или его смесей с СПГ.
Пример: Шведский проект HYBRIT уже использует гибридные резервуары, что сократило будущие затраты на переход к водороду на 40%.
Риски и окупаемость
Главный барьер — высокие стартовые вложения:
Строительство резервуара на 50 000 м³ стоит $50–70 млн.
Однако срок окупаемости редко превышает 5–7 лет за счет:
Снижения штрафов (СВАМ, национальные налоги).
Экономии на топливе и логистике.
Продажи углеродных квот.
Пример: Завод Algoma Steel (Канада) окупил резервуары за 4 года благодаря госсубсидиям и снижению импорта угля.
СПГ в металлургии — это не затраты, а инвестиции в устойчивое будущее. Помимо прямой экономии, он открывает доступ к новым рынкам, «зеленым» кредитам и технологиям следующего поколения. Как показывает практика, даже в регионах с дешевым углем (Кузбасс, Китай) газ становится выгоднее из-за растущего давления регуляторов.
Комментарии